【手回しXY軸+手動Z軸ケガキ・ポンチ・穴あけ盤の@】 |
トップページへ このページのトップへ |
(この記事の続きは2ページです。思っていたより長くなりました) |
「遠心スイッチで速度制御」、実験は成功しましたが、実用化(ホビー的にですけど)するには幅や長さを大幅に縮めなければなりません、しかしその辺は暑苦しくて寝苦しい夜を利用して思いつきました。
思いついたのは良いのですが今度は「つ・作るの面倒くせぇー」、構造は簡単なんですが、軸とかの穴あけを考えるだけで嫌で嫌でたまりません、「絶対狂うにきまってるー」、今までのように3ミリとか6ミリとか10ミリの穴ならば、少し小さめの穴をあけてから「修正する」とかいう手が使えます。
しかし完成した穴径が1ミリとかになると「センターポンチ作業」と「穴あけ作業」で絶対狂うにきまってる、これは「オプティカルセンターポンチ」を使っても狂うと思います(穴あけ時に狂う、多分)。
それも同じものを数枚ともなると、もうイヤッ、そこで頭に浮かぶのは「フライス盤」か「CNCマシン」、
cvfの工作教室様はフライス盤をボール盤換わりに使用しているようですが私は持っていない、それに作るものに対して大袈裟すぎる気がします(負け惜しみ)CNCは勿体なさすぎる(というより手がでない)。
んでどのぐらいの物を作りたいかというと、せいぜい厚さは 0.5ミリ以下の金属板、大きさは 3センチ×5センチ程度まで、枚数は 10枚程度、こんなのに好きな所に正確に簡単に 1ミリの穴があけられたら言うこと無しです。
そこで設計条件。
その辺の物で作る、(出たー)簡単に作る、金かけない、いつでもどこでも使える【手回しXY軸+手動Z軸ケガキ・ポンチ・穴あけ盤】というのを作りたいと思います(ちょっと題名長かった)。
題名はご大そうですが、中身は大したことありません、X軸とY軸送りは日曜大工センターで購入できる6ミリの長ネジ(ピッチ
1ミリの奴指定、前に間違ってインチネジ買ったことある)(恥)。
Z軸はただのシリンダーです。この中にポンチ入れたりケガキ針入れたり 1ミリの簡便ドリル入れたりするだけです。
ステッピングモーター使ったりして電動にすると面白いけど、とりあえずは手動でがんばってみます。こりゃ
1日では無理ですね、連載になりそうです(完成出来れば良いけど)。
|
【の、A】、X軸レール(土台、始まりです)
直線運動するには「引き出し用スライドベアリング」とか色々便利な部品がありますが、東京まで買い出しに行くのも面倒なので、(田舎です)アングルと戸車で作ります。ちょっと大きくなるし、精度もあまり期待できませんが、なんとか
0.1ミリぐらいに抑えてみたい・・・というか構造で補っていこうと思います。
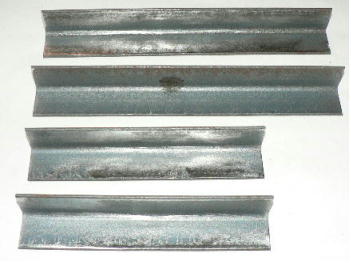
とりあえず「その辺にあるもの」です。 3の 25×25アングルです。なんにも考えないで 210ミリと 140ミリに 2本ずつ切りました(すでに寸法間違えている気がする)。
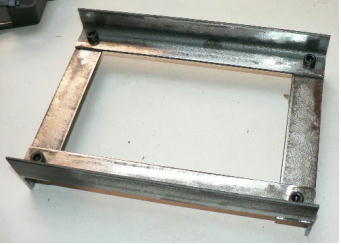
これがX軸(一軸)テーブルのレールになります。お題は長ったらしい名前ですが、新たに機能が増えて、さらに長くなりそうです。今のが完成してから追加します。
本日は作業時間 10分(結構忙しいので)。
B
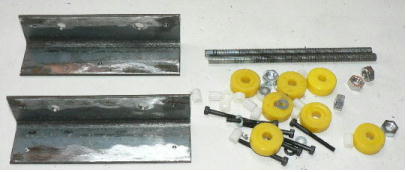
X軸の台車の材料です。黄色いのは戸車を分解した車輪です。
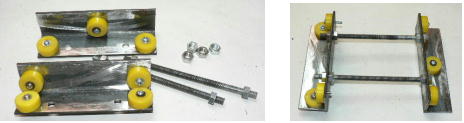
なんだかあちこち間違って何度も穴をあけ直ししました。
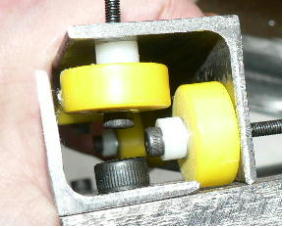
決定的に失敗、レールに車輪がのっかりません、なーにやってんだか。
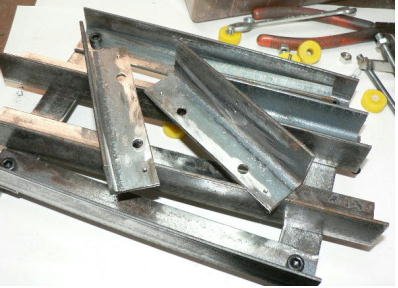
でもって材料刻み直し、五右衛門のセリフじゃないけど「またつまらないものを切ってしまった」。
作業場、ふと温度計見たら 36度、なんだか体が揺れてます。これはヤバイ、2度UPなんてとんでもない、これでやめます(居間に戻って血圧はかったら174、普通は130ぐらいなのに、そういえば頭が痛い)。
C
失敗にもメゲす再開です。
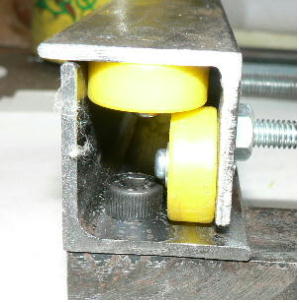
3の25×25ミリアングルから単純に 3の30×30ミリアングルにレールを取り換えました(実はなんとか使おうとして色々やったけどダメでした、 1時間ぐらい損した、引き際って難しい)。
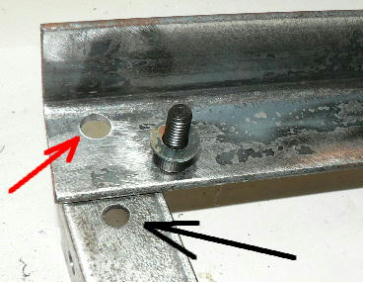
レールの四隅を止める穴です。一か所だけ 8ミリ(赤矢印)であけてます(黒矢印は
6ミリ)レールの幅の調整をする為です。
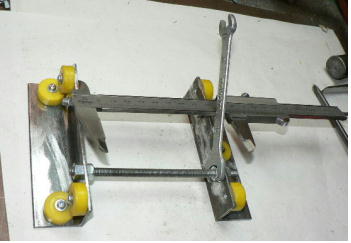
X軸台車の車輪の幅を正確に合わせます。
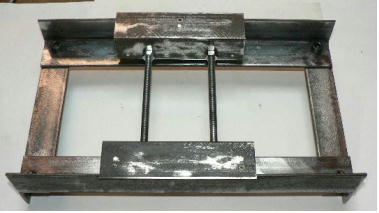
X軸レールと、乗っかる台車が完成しました。実はアングルをこのように使うのはマズイ事です。理由は「日本工業規格の二等辺山形鋼の断面寸法図」を参照するとわかります。アングルの内側をこんな風に使ってはいけないのです。しかし「ホビー工作」ならかまいやしません。
実はアルミアングルならOKです。アルミアングルは「均等な厚さ」だからです(高いので私は使わない、だって失敗したらもったいないもの)。

次はX軸の駆動部分を作りたいところですが、Y軸レールが無いと取り付けられないので、ちょっと我慢です。
D
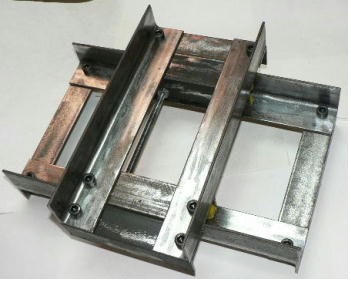
Y軸レールがX軸台車に乗っかりました。
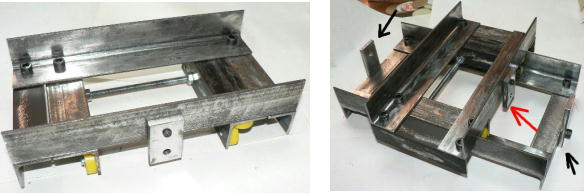
左写真の真ん中の平鉄が、(赤矢印も同じ部分)X軸台車送りのステー(雌ネジ)です。黒矢印は送り装置のベース部分です。この中に長ネジを入れて台車を動かす訳です。
6の 1.0ミリピッチですから「1回転で 1ミリ」動きます。市販の長ネジですから精度は結構高いと思います。ホビー工作ですから「ボールネジ」は使っていません(本当は使いたいけどもったいない?)。
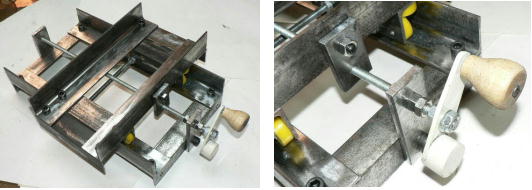
X軸送り装置はまだ仮設状態です。転がっていたハンドルを仮に取り付けてみました。この状態で回すと「旋盤等」とは逆に動いてしまいます。その辺の必要な部品はこの機械がある程度完成しないと作れません。
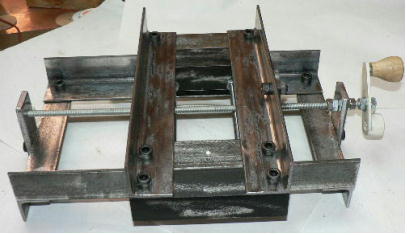
X軸送りは一応完成です。あちこち仮設ですけど動きます。
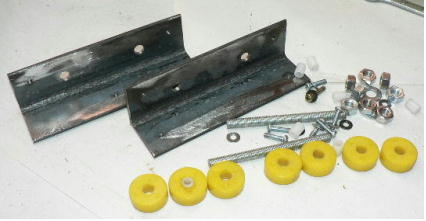
次は Y軸台車です。 X軸台車で経験していますので、割と簡単に加工出来ました。全部品です。
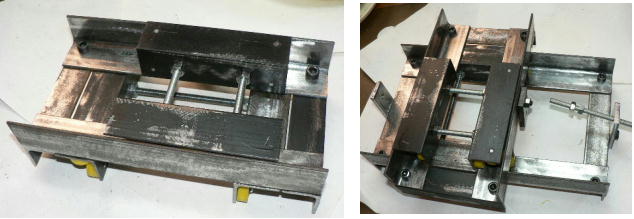
Y軸台車を組立ててレールに乗せました。台車に作業天板を取り付け、送り装置を作ればXYテーブルは完成です。天板には蟻溝?を付けたいところですが、ボコボコ穴があきそうなので、取り換えが出来る構造にしようか悩んでいます。
E
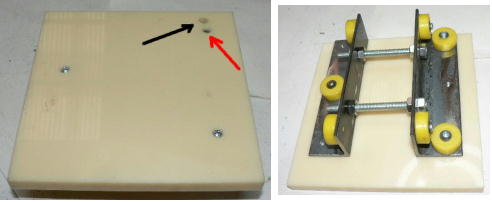
作業テーブルです。最初厚手のベニヤ板で作ろうと思ったのですが、ここまでアングルと平鉄と戸車、それから長ネジ、あまりにも「地味」なので、一点豪華趣味ではないけれど、クズ材料入れにABS樹脂の切れ端があったので使ってみる事に(寸法いい加減)。
しかし、しばらく触っていなかったので穴あけに失敗しました。 2.5ミリであけたあと、。
6ミリで皿もみ(この時点で間違っている)しようとしたら、「吸い込まれるように貫通穴」(黒矢印)。
あわてて少し離れた所に穴あけし直ししたらまたもや貫通穴寸前、(赤矢印)ナメてかかるとろくなことがありません。
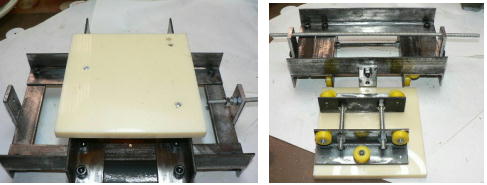
乗っけてみるとちょうど良いあんばいです。
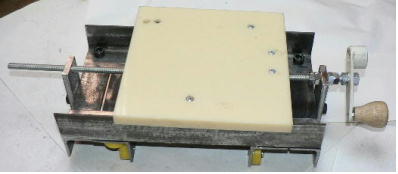
なんとかY軸台車とテーブルを完成させました。ためしに手で回してみると不都合発見、長ネジが少し湾曲しているようで、1回転ごとに台車がわずかに揺れます(大体
0.5ミリぐらい)やっぱりこういうところは「ボールネジ」とか使わないと精密さが出ないですね。
その辺のところはあとで考える事にします(今はとりあえず完成させることに集中)。
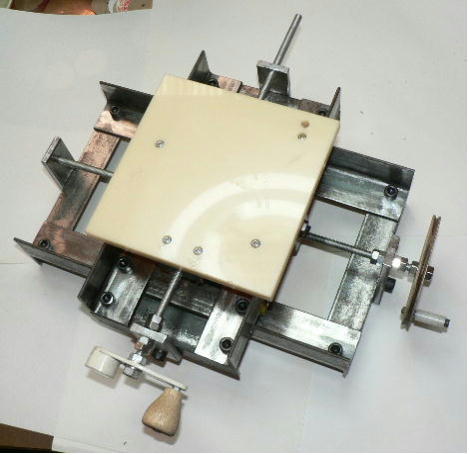
手送りXYテーブル完成しました(Z軸はまだです)まだ送りハンドルや、長ネジの「ガタ」解消は取り付けていません、回転方向の修正もまだです。ところでこの手のガタを「バック ラッシ」と表現しているページが多々あります。私が古いのかどうか知りませんが、メカニズム辞典によるとバック ラッシとは「一対の歯車をかみ合わせた時の歯面間の遊びをバック ラッシ(back lash)という」とあります。長ネジも歯面間なのかしら?、どなたか「そうだ!!」とか「ちがう!!」とか言ってくださるとすっきりするのですが(私はただのガタだと思ってた)。
ところで大変な事態となりました。「めんどくさい・やりたくない・昼寝していたい症候群」が発病しそうなのです。これにかかるとなにもしたくなくなります。予防薬はビールか缶酎ハイかな?。
原因は「トロ車」や「スライドベアリング」等を使わないで戸車なんか使っているからです。 14個も使っています。これはストレスです(なんでこんなことを始めたんだろう・・・という疑問が、なんか最初の目的がなんだったのか忘れそう)。
【とりあえず完成】
あちこちまだ未完の部分がありますが、おいおい追加することにして、とりあえず使えるようにします。

Z軸全部品です。Z軸といっても、ただ上下する針を支えるシリンダーだけです。ドリル付きモーターを取り付ける事も出来ます。赤矢印は「手回しベース」のアーム先端部分です。黒矢印は10ミリの丸棒に3ミリの貫通穴をあけた物です。ここにケガキとかポンチ等が入ります。
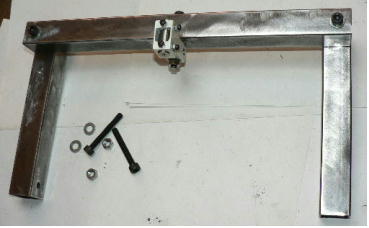
Z軸は頑丈に作る必要があります。25×25ミリ角パイプをつかって鳥居を作りました。
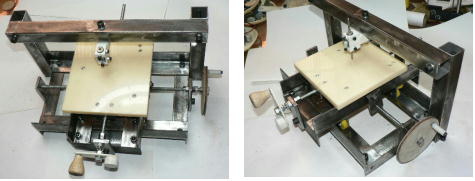
一応完成です。
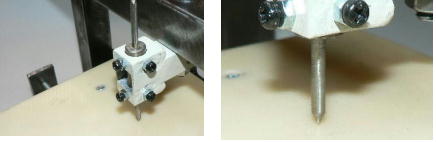
ポンチ針を入れたところです。
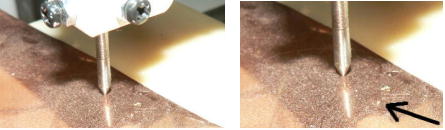
あちこち作らねばならない部分がありますが、どうしても一度使ってみたくて「ポンチモード」をやってみました。まず適当にポンチします。そしてX軸を10回転、10ミリのところで、さらにポンチします。
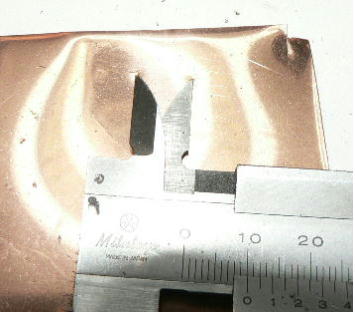
何の事はない、10ミリ離して2ヵ所刻印しただけです。まぉ当たり前ですが、ノギスで測っても10ミリ離れています(当たり前だっつーの)しかし、フリーハンドでやろうとしたら正確に打つのはなかなか大変だと思います。こいつを使えば「実に簡単」に何度でもできます。
この「ポンチモード」作業だけでも大助かりですが、さらに「ケガキモード」、「ドリル穴あけモード」そして最後に追加する「分割モード」が出来るようになります。絶対ホビー工作したくなると思います。 |
続きは2ページです。
(スクロールが長くなったので)
|
|
【ピン歯車外周穴あけ盤】 |
トップページへ このページのトップへ |
(手回しベースを利用した物を思いつきました)
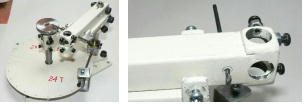 画像を縮小させすぎました。
色々考えたんですが、結果的に非常に簡単に実現してしまいました。あれこれやっているうちに「コイルスプリング製造時にハンドルを固定(というか止める)する横穴」を利用することを思いつきました。
主軸アームをもう
1個使います。これにより本体をテーブル等に固定する必要さえなくなってしまいました。今、横穴に先を尖らせた
2ミリのピアノ線を差し込み、位置を決めてます(右写真)。
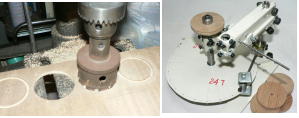 素材円盤です。寸法はローラーが 4ミリ、ピンが 2ミリなので「ピッチ
6ミリ」です。歯数は 24なので、 (4;+2)×24÷π=約 45.86ミリ(実行直径)。 内直径は
4ミリ引きますので 45.86-4=41.86ミリ、丁度 48ミリのホールソーがありましたので(こいつで抜き取ると、約
42ミリのはず)ベニヤから作ります。実際には 41.5ミリでしたが、
0.14ミリなんてどーでも良いのでこれで行きます。
右写真は準備ができたところです。
【穴あけ開始】 A
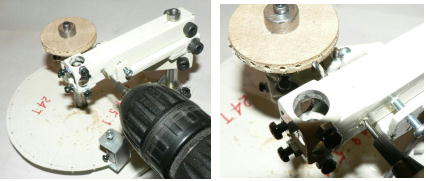 電気ドリルにくわえた
2ミリのキリサキで穴をあけていきます。だいぶ前にやった時は縦型でしたが、今回は手回しベースの関係で横型です。
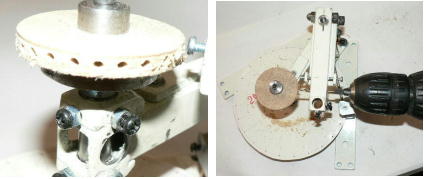 24ヶ所終わりました。右の写真は真上からの物です。位置関係がわかりやすいかと思って撮ってみました。
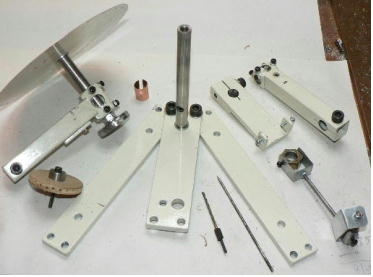
今回使用した全部品です。ちょっと多すぎだと思いました。あとで無駄な部品をなくしていこうと思います。
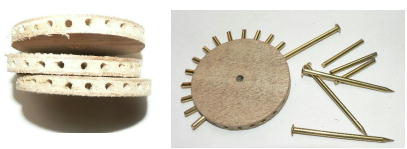 穴あけが終わったので、太さ 2ミリの真鍮釘を打ち込み始めました。しかし真鍮とはいえ、
2ミリともなると、切断にはかなりの力が必要です。それにかなり重くなりそう、それから「なんか穴の列が乱れてる」っポイ、間隔はあっているようですがなんか変。
原因を調べたら「ドリルキリサキ」でした、キリサキの側面でパイプが削れてしまったようです(当然間隔もずれてる?)電気ドリルを水平に保持しての穴あけは結構きつい、24ヶ所もやっている内に馬鹿穴にしてしまったようです。そんなこんなで真鍮釘は止めることにしました(穴あけ方法も変えます)。
今やっているのは「中間ギヤ」です。そんなに力が掛かるとも思えません、そこで「竹ひご」でやってみようと思いました。しかし
2ミリの竹ひごはその辺にありません、そこで「焼き鳥の串」を使ってみることに。
スーパーで買ってきた物は直径
2.5ミリぐらいでした、(2.5ミリよりちょっぴり太い感じ)このまま使うとなると計算し直して新たに作らなければなりません、直径も大きくなってしまうので、串を削る事に。
しかし「どうやって削る?」、なんか簡単な方法があったような。
|
|
【外周切削盤】
(手回しベース+箱入りサンダー娘で作る) |
トップページへ このページのトップへ |
あまりに簡単なので要点だけUPします。
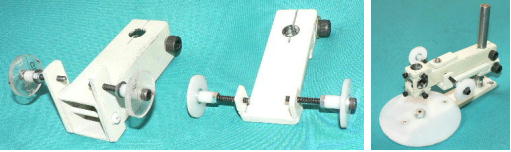
まず「主軸アーム」の「微動送り」の背の低いのを作りました。左の写真左が前に簡単に作った奴です。右が今回の物です。そして右の写真がセットした状態です。丁度スペースシャトルがブースターに乗っかったようなあんばいです。
これにより、アームは約 10ミリほど微動送りの上で動きます。ネジは 3ミリ、ツマミ円盤
1回転で 0.5ミリ送られます(今回は微動送りではなく、半径を決めるストッパーとして働きます)。
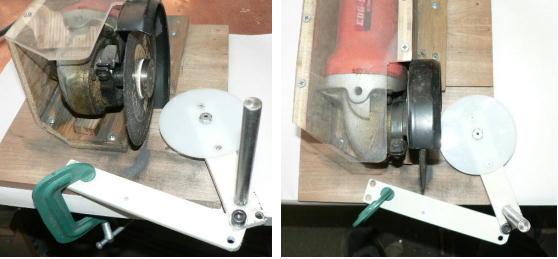
箱入りサンダー娘の台の上に手回しベースの土台部分をクランプで固定します。左が斜め上から、右が真上から見たところです。位置は切断砥石からの「具合見」です。
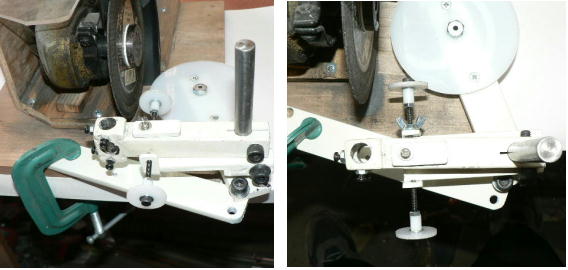 微動送りを支柱に入れ、主軸アームをその上から入れます。高さは切断砥石の中心から少し下です。向こう側の微動送りをギリギリまで戻し、蝶ナットで固定します。もちろん円盤の仕上げ半径です。手前の送りは使いません、目一杯アームが移動出来るように広げておきます(円板の仕上げ半径は、向こう側のツマミネジで決めます。切削中動かないように蝶ナットでロックしています)。
外周切削盤なんて言っていますが、準備は「たったこれだけ」です。これで
20ミリから 140ミリ(直径)ぐらいまでの円盤が切削出来ます。もっともセットする関係で、ある程度「円」に近い形に準備する必要がありますが。
【こいつは失敗】
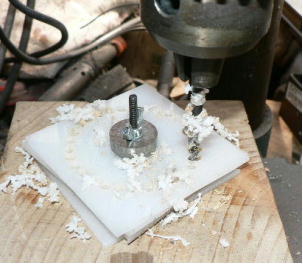 前に作った原盤を元に「3枚」いっぺんに穴あけしてみました。材料は塩化ビニールの板です。かなり柔らかい、結果的に大失敗、よそみしながらやったら原盤の穴の縁を削ってしまった。
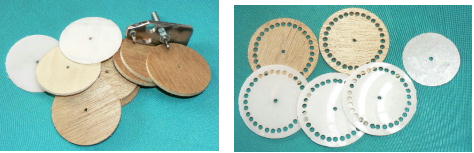 ついでに厚さの違うベニヤ板でも穴あけしてみました。素のままのベニヤではダメだろうとは思いますが、物は試しです。
 原盤を塩化ビニールの板なんかで作っていたのではダメに決まっています。見事に「目ん玉つながりのおまわりさん」(おそ松くん)みたいになってしまいました。それから中心で
3ミリのボルトナットで押えていただけでは、多数の穴あけしているうちに「わずかずつずれるようです。そこで矢印のように初めに 2ヵ所穴あけした所に
4ミリのスぺーサーを突っ込み、「ずれ」を止めてます(つまり結構失敗してる)。
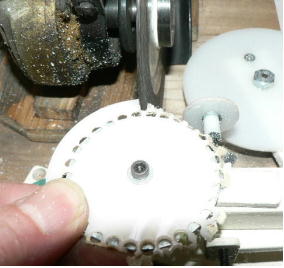 外周切削盤にセットし、余分な部分を切削します。ここでまたまた失敗、
60ミリでくりぬいたため、6ミリ以上切削するハメになってしまいました。これはかったるい、ホールソーは直径 50ミリぐらいにすべきでした(仕上がり寸法は直径
47.8ミリぐらい)。
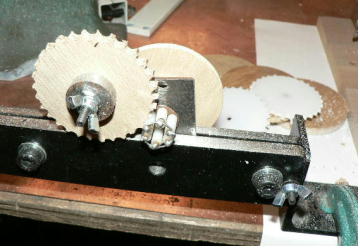 おバカテストです。ベニヤで作ったスプロケットをセットして回してみました。始めのうちはなんとかでしたが、すぐにダメになってしまいました。素のベニヤではこんなものでしょう。
それから原盤ですが、やはり鉄で作らないとすぐに馬鹿穴になってしまいます(当たり前)しかし「鉄」でもそんなに持たないと思う、ここはやはり別な手(思いついてる)をやってみます。それと主軸がブレてるボール盤などを使っていては
0.1ミリ以下の誤差で押えようなんて愚の骨頂だと悟りました(たとえ原盤を精密に作っても、すぐに馬鹿穴になる)。
|
|
【ローラースプロケット制作盤】 |
(ボール盤+手回しベース+分割装置) |
トップページへ このページのトップへ |
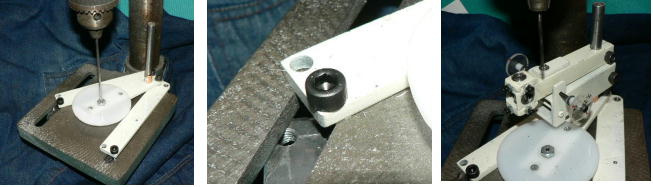 ボール盤のテーブルに手回しベースをボルト締めします(左と中)このときボール盤の芯と手回しベースのテーブル中央は同一垂線になるようにします。手回しベースの「土台穴」はこういうときのためにあけた訳ではありませんが、丁度具合よく止まりました。そしてメインアームと「アーム微動送り台」を取り付けます(右写真)。

メインアームのシャフト穴は、「分割盤」の中心穴になります。どのような構造にしようか悩んだんですが、そんなときは「心の赴くまま」こんなの作りました。「叩きバメ」です。あとで気が付いたんですが、フラットバーはいらなかった(貫通穴はこの段階ではあけないので)(実はこれが重要な意味をもっていた、あとでわかった)
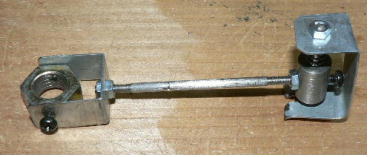
分割指示針も一工夫しました。
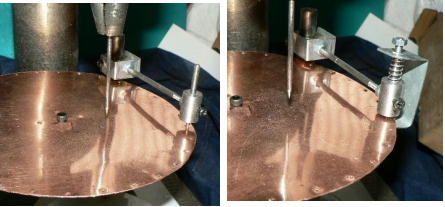 前に使った時、この分割支持針が打撃の時、毎回飛び上がって離れてしまうのです。今回はボール盤なのであまり飛び上がったりしないと思うんですが、もしずれると厄介です。そこでスプリングで円板に押し付けるような細工をしました。これもその場の思いつきです。あとでもうちょっと使いやすい構造を考えたいと思います。
いよいよ円盤の中心とドリルキリサキとの距離を正確に調整すれは゛準備完了です。 その距離は 5×30÷3.14÷2=(約)23.88ミリです(半径)。
【ローラースプロケット制作盤作業開始【】A
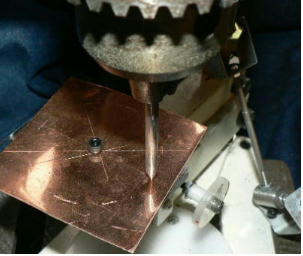 まずは半径 23.9ミリぐらいのところにボール盤の針をあわせます。ところで私のボール盤はワゴンセールで
5800円で買ったせいか、静止状態と回転中で芯の位置が
0.5ミリほど違います。なにしろチャックを引っ掴んでゆすると「ガタガタ」します。まったく困ったもんです。それでこの写真は回転させながら印を付けてます(こんなボール盤ではフライスに改造なんて夢のまた夢)。
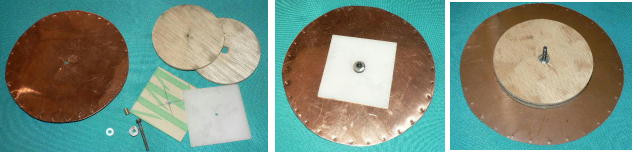 分割円盤と加工物の取り付けです。一度順番をまちがえて加工物を無駄にしてしまいました(それと時間も)。
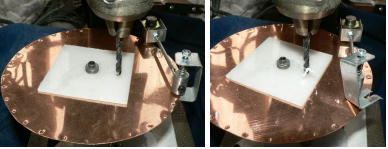 分割針をセットしていよいよ穴あけ開始、ここで
10ヵ所ぐらい穴あけしたところで重大なミス発見、考えてみたら当り前のことですが、加工物をしっかり固定しないと穴が滑ったり斜めになったりすることです。前にフラットバーを付けて、「無駄な作業をしてしまった」なんて書きましたが、とんでもない、とても重要な事だったと今頃きずきました(分割円盤の針で十分だと思っていた)。
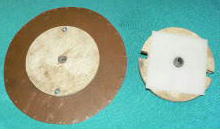 30ヵ所穴あけ終わりました。捨て板をはずしてから写真撮れば良かった、なんだか白くてわけのわからない写真になってしまいました。んでこのあとアクシデント、前に作った
6Tのギヤが行方不明になっていたのです。いやはや「時間はないわ早く試してみたいわ」で心が急く。(私はサラリーマンなので遊んでばかりはいられない)
結局見つからず
6Tを新たに作る羽目になるやも、(ガクッ)しかし 6Tなんか「あっという間」に作れなくてはロボットなんかは作れません、がんばるぞー。
【ローラースプロケット制作盤】のB
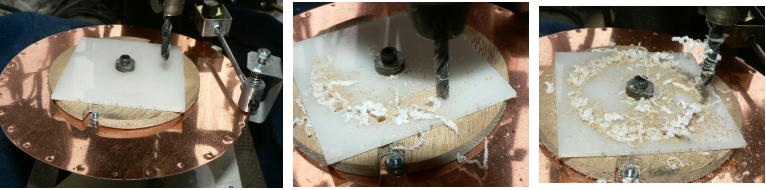 いよいよ
30ヵ所の穴あけスタートです。こういう穴あけのやり方は初めてです。無駄に緊張してしまってつい加工物を押さえたり油をやるのを忘れてしまいました。
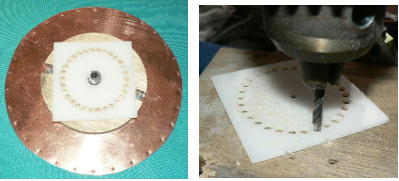 30ヵ所終わりました。なんかバリとか多そうなので、手動でさらいました(右写真)。
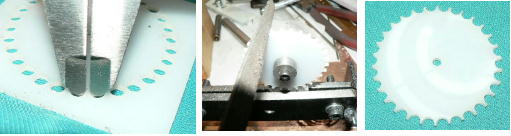 ちょっとわかりずらいですが、穴と穴の間隔をノギスで測っています。ちゃんと出来ていれば 1.0ミリのはずです。
20ヵ所ぐらいはOKでしたがあとは 0.8ミリとかひどいのになると
1.6ミリのところがありました。あまりにひどいのでこれを「マスター」にするのはやめて外周を切削し、スプロケットとして完成させました。
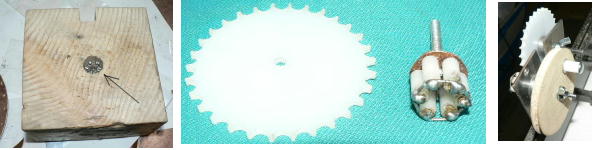
行方不明の
6T、なんと角材の真ん中の穴にはまっていました。40分ほどさがしてもう諦めかけていたところです。 手で組み合わせてみたところ、なんとも言いようがない「マズさ」です(この時はそう思った)ボックスを作って組んでみる元気も出ません、ふと、工作ベース300で挟んでみようかなと思い立ち、(この辺はしつこい)6Tにハンドル付きのプーリーモドキを付けて手で回してみました(右写真)。
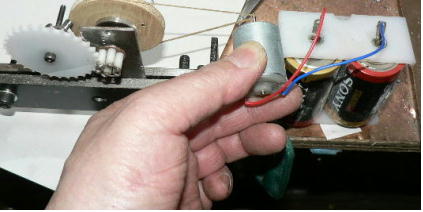 なーんかヨサゲ、そこでマブチの280モーターで回してみる事に(5対1にプーリーが大体 25対1で
125対1ぐらいです)。
なんか3Vで快調快調、音も静かだし(モーター音の方が高い)動力伝達能力も今までの(過去の)とは段違いです。実に快適に途中引っかかるような動作もありません、280ですからトルクはまったく期待できませんが、模型工作なら市販のギヤボックスセットにも引けを取らない感じです(もっと色々手こずるかと思った)。
マスターを作っておけば複製にはボール盤だけで「分割」とか余計な装置は一切いりません、材料も下敷きでもベニヤでもアクリルでも好さそう、強度だって幅を広げれはOKだし。
これは実用化が今一だった「差動減速装置」にも応用がききそうです。これで長年の悲願だった「赤貧サーボ」に2歩も3歩も近づきました。なんたって材料費はタダに近いしギヤ比は自分で決められるし言うこと無しです。
つまり「 大成功 」バンザーイ。
【ローラースプロケット少量生産への道】
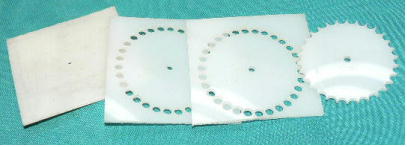 ローラースプロケット制作盤で作った物は「マスター」というか「原盤」になります。これを元にすれば「マスター1枚に付き10枚」ぐらいは複製出来ると思います。10枚以上になると、たぶんマスターの穴が広がってしまい、誤差が大きくなると思います(マスターから子マスターを作っておけば良いかも)。
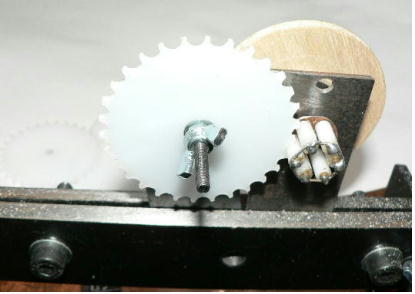 これは前の奴ではありません、複製です。ところでこういったものは、大抵はヤスリで仕上げないと使えないものがほとんどです。しかしいちいちヤスリがけはかったるい、そこで考えました。「なぜやすりがけは必要か
? 」、答え「バリが出ているから」、それだけかな ?
、実はこのローラースプロケットもインボリュート曲線がちょっと絡んでる、それではインボリュート曲線が絡む部分を無くしたらどうか ?
、ってんで外周切削をローラーの中心まで(2ミリ)削ってみました。
で、そうやって作ったのがこの写真の奴です。ヤスリ仕上げとか何もやっていません、結果は上々なんの問題もなく伝達しています(ローラーのすべり摩擦が面倒な部分を解消している・と思う、この辺は突っ込みどころですがご勘弁を)。
そこで次回はバリの出ない切削が出来る「外周切削盤」を「手回しベースと箱入りサンダー娘」の組み合わせで作ってみたいと思います(これでもパリは出るけど指でコソゲ落とせる)。
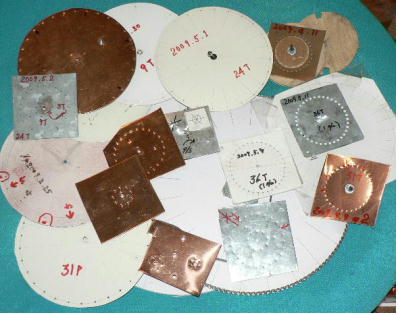
これは今回のネタの元である今まで作った「分割円盤群」です。こんなに作っていたとは思いませんでした、これって無駄な努力だったのかなぁ、産みの苦しみと思いたい、何しろ使えるものはこの中でたった一枚だもんね(左上の奴です)。
|
|
【1軸習い切削盤】 |
トップページへ このページのトップへ |
1軸習い切削盤とはカギコーナーで家の合鍵などを作ってもらうときに使う機械からヒントを得た工作機械です。違いは左右の移動を軸にして回転させることです。これにより円盤関係のコピーが出来ます。 |
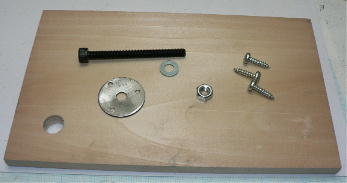 _ |
土台というかベースです。大きめの平ワッシャは工事中の歩道橋現場で拾いました。目隠し板を止めるための物のようです(取り替え工事中、30枚も拾った)6ミリのボルトが穴のあいたところに取り付けられます。Y軸の支点のような物です。各寸法は適当です(ただの鉄板で作っても良いです)。
|